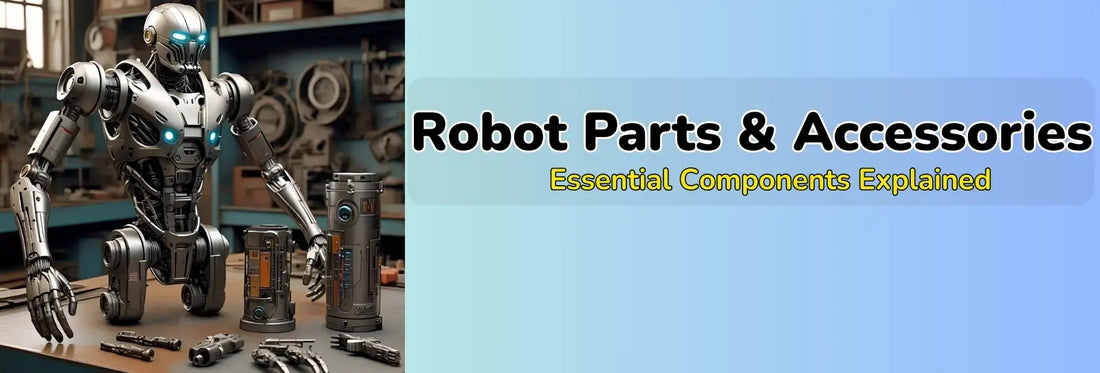
Robot Parts & Accessories: Essential Components Explained
IEM RoboticsTable of Content
-
Robot End Effectors
- Significance of End Effectors in Robotics
-
Robot Controllers
- Robot Batteries
- Robot Base or Mounting Systems
- Robot Safety Components
- Conveyor Belts: Moving Automation
- Final Thoughts
Robots are part of everyday industry, research, and even life. They are employed in various sectors, from manufacturing and healthcare to space exploration and the military. Robots' efficiency, accuracy, and automation capacity are essential in most industries.
But to comprehend how robots work, one must examine their essential components. Every component has a specific function in the robot's operation, which affects its performance, stability, and functionality. This blog offers a detailed and lengthy overview of robot parts. It also offers the technologies that enable it to function seamlessly.
Whether you're a young robotics engineering student, a scientist, or simply a robotics enthusiast, understanding these components provides valuable insights into planning, building, and optimizing robots.
Robot End Effectors
End effectors are key elements in robotics. They serve as a robot's hands or tools. They are installed at the tip of robotic arms, allowing the machine to carry out various tasks, such as holding objects, welding, and painting. End effectors are available in multiple forms, depending on their use and the level of precision needed. Types of End Effectors in robot parts:
Grippers
Grippers are one of the most widespread end effectors and are usually utilized for manipulating and holding objects. Some examples include:
● Mechanical Grippers: They apply fingers or jaws to grasp items and are best used for industrial assembly and automation lines.
● Vacuum Grippers: These grippers use suction cups to move and position items, are found on logistics and warehouse robots.
● Magnetic Grippers: They are used in magnetic fields to lift metallic objects. They are frequently used for transporting materials and handling scrap in robot parts.
● Adhesive Grippers: The grippers use specialized sticky substances to grip fragile or abnormally shaped items in soft robotics.
Specialized End Effectors
For advanced and intricate applications, specialized end effectors are designed, such as:
● Bio-inspired Grippers Imitate human or animal hand motions and are used in sensitive applications such as surgery or food handling.
● Multi-functional End Effectors: Set up to change between tools automatically, enhancing efficiency in dynamic situations.
Adaptive and Intelligent End Effectors
Advanced robots now employ intelligent and adaptive end effectors with sensors and AI-based controls. They include:
● Tactile Sensors: Allow robots to regulate grip tightness according to object delicacy.
● Vision-guided End Effectors: Utilize cameras and image processing to sense and handle objects precisely.
● Force Feedback Mechanisms: Allow real-time force adjustments, improving the accuracy of robotic surgery and assembly lines.
Significance of End Effectors in Robotics
End effectors are crucial in determining a science robot kit functionality and versatility. Their selection depends on factors like:
● Application Requirements: Whether the task involves lifting, assembling, welding, or packaging.
● Material Properties: The shape, weight, and surface texture of objects being handled.
● Environmental Conditions: Operating in extreme temperatures, underwater, or vacuum environments.
Robot Sensors
Sensors play an essential role in robotic systems. They enable robots to sense the world, collect information, and make wise choices. Sensors also would allow robots to sense objects, move autonomously, and safely interact with objects and people.
Vision Sensors
Vision sensors enable robots to "see" and interpret visual information. They consist of:
● Cameras: Applied in machine vision tasks to recognize objects, inspect quality, and navigate.
● Stereo Cameras: Enable depth perception, making 3D mapping and avoiding obstacles possible.
● Infrared Cameras: Employed in night vision applications, thermal imaging, and heat signature detection.
Position and Motion Sensors
These sensors assist robots in comprehending movement, orientation, and position. Some examples are:
● Encoders: Monitor rotation and motor position to ensure accurate control of movement.
● Inertial Measurement Units (IMUs): Identify orientation and acceleration, essential for humanoid robots' balance.
● Gyroscopes: Assist stability in drones, robotic arms, and self-driving cars.
Proximity and Range Sensors
Proximity sensors enable robots to sense objects close by without touching them. Examples of robot accessories are:
● Ultrasonic Sensors: Use sound waves to determine distance, typically employed to avoid obstacles in autonomous robots.
● Infrared Sensors: Use infrared radiation to sense objects, utilized by line-following robots and proximity sensing.
● LIDAR (Light Detection and Ranging) offers highly accurate distance measurement and 3D mapping. It is extensively used in autonomous vehicles and industrial robotics.
Environmental Sensors
These sensors assist science robot kit in working under varied conditions by sensing temperature, humidity, and other environmental parameters. Some examples are:
● Temperature Sensors: Avoid overheating in robotic systems.
● Gas Sensors: Identify harmful gases in industrial and dangerous environments.
● Barometric Sensors: Utilized in drones and self-driving vehicles for height sensing.
Robot Controllers
The robot controller is the system's brain. It receives inputs, makes decisions, and sends commands to actuators and sensors. The controller executes tasks accurately and enables communication among different robot components.
Robot Controller Types
Some of the types of robot controllers robot parts are :
● Microcontrollers (MCUs): Employed in basic robotic applications, such as Arduino-based robots. They are responsible for basic input-processing-output operations.
● Microprocessors: Used in more sophisticated robotic devices needing greater computing power, e.g., Raspberry Pi or industrial automation robots.
● Programmable Logic Controllers (PLCs): Used in industries for industrial automation purposes of real-time control and logic-based decision-making.
● Industrial Robot Controllers: For heavy-duty manufacturing robots, with motion control, safety, and multi-axis coordination.
Robot Controller Functions
● Motion Planning: Calculates the best path of movement for the robot.
● Sensor Integration: Retrieves and processes environmental sensor data.
● Real-time Decision Making: Reconfigures movement and responses based on real-time conditions.
● Communication and Networking: Facilitates communication with other robots or control systems using Wi-Fi, Bluetooth, or industrial Ethernet protocols.
Advanced Robot Control Systems
● Model Predictive Control (MPC): Employs real-time information to predict and optimize future movements.
● Distributed Control Systems (DCS): Enables multiple controllers to cooperate in a network.
● Autonomous Control Systems: Allow completely automated robots to function without human interaction.
Robot Batteries
Batteries are the primary energy source for most robot accessories, providing uniform operation. Energy density, rechargeability, lifespan, and weight affect the correct battery selection.
Batteries Used as robot accessories
Lithium-ion (Li-ion) Batteries
● Positive aspects: Large energy density, lightweight, and high lifespan.
● Use: Utilized in drones, autonomous cars, and mobile robots.
● Drawbacks: Costly, needs protection circuits to avoid overheating.
Lithium Polymer (LiPo) Batteries
● Advantages: More elastic shapes, high discharge rates, and lightweight.
● Applications: Used in robotics competitions and high-performance drones.
● Challenges: Overcharging sensitivity, swelling, or fire risks.
Nickel-Metal Hydride (NiMH) Batteries
● Advantages: Environmentally friendly and safer than Li-ion.
● Applications: Employed in education robots and industrial bots of the middle range.
● Challenges: Low energy density and comparatively heavier.
Lead-Acid Batteries
● Advantages: Low cost and delivers high power output.
● Applications: Industrial robots, warehouse AGVs (Automated Guided Vehicles).
● Challenges: Heavy, shorter lifespan, and needs constant maintenance.
Robot Base or Mounting Systems
A sturdy and well-engineered base is essential for the robot's balance, movement, and interaction with the surrounding world. The base provides structural stability and dictates the robot's general functionality.
Fixed Bases
● Fixed Robots: Installed in factories, the robot has to execute repetitive functions, including robotic arms used to manufacture automobiles.
● Anchored and Bolted Bases: Hold the robot in place firmly for accurate operations.
Mobile Bases
● Wheeled Bases: Employed in autonomous cars and warehouse robots for smooth transportation.
● Tracked Bases: Offer better stability and traction on rough surfaces, e.g., search-and-rescue robots.
● Legged Bases: Employed in biped and quadruped robots to traverse challenging terrain.
Robot Safety Components
Robot safety is of significant concern where human interaction exists in a surrounding that comprises humans and robots. Safety components will help prevent robot malfunction and accidents in a given operational area.
Emergency Stop Mechanisms
● Physical Emergency Stop Buttons: They are stop buttons used by hand to cause immediate robot shutdown.
● Software-Based Stop Systems: Included within control software that prevents operation on detecting system breakdowns.
Collision Detection and Avoidance
● Proximity Sensors: Sense the surrounding objects to avert collision.
● Force Sensors: Detect the impact and compensate for movements accordingly.
● Vision-Based Safety Systems: Employ cameras and AI to detect obstacles and halt motion when required.
Protective Enclosures and Shields
● Cages and Fences: Employed in industrial robotics to isolate robots from human workers.
● Transparent Safety Shields: Permit observation while maintaining protection from moving components.
● Soft Covers and Padding: Used on collaborative robots (cobots) to reduce the risk of injury.
Fail-Safe Mechanisms
● Redundant Power Systems: Make robots operate even when one power source fails.
● Self-Diagnostic Systems: Identify internal faults and shut down to avoid damage.
● Backup Control Systems: Provide manual takeover in the event of system failure.
Conveyor Belts: Moving Automation
Conveyor belts are critical to robotic systems, particularly in the manufacturing, logistics, and material handling sectors. They enable automatic transportation of materials, minimizing the need for human labor and increasing efficiency.
Types of Conveyor Belts
● Flat Belt Conveyors: The most widely used type, featuring a continuous belt for smooth movement of materials. They are prevalent in food processing, packaging, and assembly lines.
● Modular Belt Conveyors employ interlocking plastic segments, providing flexibility and simple maintenance.
● Inclined Belt Conveyors typically found in warehouses, usually objects from one height level to another.
● Roller Conveyors: They employ cylindrical rollers rather than belts, typically found in distribution centers.
Advantages of Conveyor Belts in Robotics
● Efficiency: They mechanize material handling, speeding up production.
● Consistency: Provide consistent movement of products, minimizing errors.
● Integration with Robots: Industrial robots are used by many in conjunction with conveyor belts for picking, placing, and sorting tasks.
● Customization: Can be customized according to weight, speed, and material type being carried.
Final Thoughts
Robots are intricate machines with different fundamental parts, each vital to functioning. Knowledge of these components, from the structural elements and actuators to power supplies and control units, is key to designing and enhancing robot parts. Conveyor belts are critical in automation and facilitate the smooth incorporation of robotic operations in manufacturing and logistics industries.
Whether you are a robotics enthusiast, engineer, or student, thoroughly understanding these parts will enable you to construct efficient and effective robots.